
Length of bend - equation for length of arc, based on bending radius through centerline a. Bend angle - number of degrees greatly affects raw material calculations 5. The bend radius of a tube is the radius measured to the tube’s centerline. Radius of bend - decided by the space the part fits in, dies available 3. The fix: You can reduce the stress by using a larger.
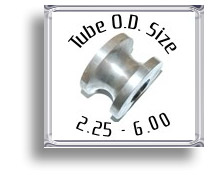
(0.551 × 0.16), the inside bend radius changes to 0.088 if the die opening is 0.972 in. When the flattening becomes excessive, it is a defect. When your die opening changes, so does your inside radius. When this happens, the tube flattens on the outside radius (see lead image). Depending on the tube diameter this could be a very large multiple but again moving away from the standard 2 x D invites tooling charges. Stainless Steel Tubing Bend Radius Chart. There comes a point at which the stress on the outside radius overcomes the ability of the tubes cross-sectional shape to support it. It is possible to have a tighter bend radius, even as low as ½ x D, although anything below 2 x D will usually require costly tooling and probably mandrel bending.Īt the other end of the scale, the maximum draw bend radius is not dictated by the performance of the tube but more by what tooling it is feasible to fit onto the bending machine. What that means is that if you have a tube OD (outside diameter) of 20 mm then the bend radius to choose, if you can, is 40 mm. When we talk about bend radius it refers to the radius measured to the center line of the tube.Įvery CNC pipe/tubing bending machine will have a different set of draw bend radius tooling based on previous jobs that they have done, but by far the most common will be in line with the first rule of thumb The standard draw bend radius is 2 x D
